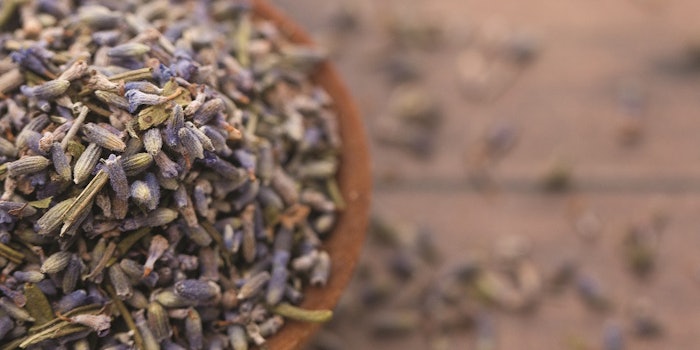
The art of extractions is an intricate, yet vast and booming, industry with many variables to consider, including maximum efficiencies, cost and quality of end-product. There are many tried-and-true solvents used by the flavor and fragrance industry, but openness to explore new and better alternatives can lead to more productive and/or more economical processes. Here we explore why bio-derived n-butanol (herein referred to as bio n-butanol) is an often overlooked, yet incredibly effective, and high-performing solvent for the extraction of essential oils and other lipophilic molecules.
So how does bio n-butanol stack up to other traditionally used solvents for extraction, such as ethanol or hexanes? In comparison to ethanol, bio n-butanol has a lower water solubility than ethanol; this results in fewer drying steps for the extracted product. When performing extractions where water may be present, the extraction with bio n-butanol will be biphasic with little from the aqueous layer entering the organic bio n-butanol layer. In addition, bio n-butanol is a more stable solvent compared to ethanol, which is notoriously hygroscopic and easily picks up water during normal work. Bio n-butanol has a lower water solubility than ethanol, but unlike a purely nonpolar solvent (e.g. hexanes), bio n-butanol maintains the polar solvency characteristic of alcohols. Further, unlike ethanol, bio n-butanol is not subject to ATF (Bureau of Alcohol, Tobacco, and Firearms in the US) making procurement and storage of bio n-butanol less burdensome.
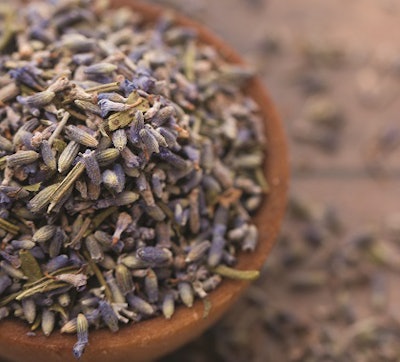
When compared to hexanes, bio n-butanol has a lower vapor pressure and by extension, bio n-butanol is much less volatile than hexanes (see T-1). Bio n-butanol has a higher Lower Flammability Limit (LFL) than hexanes; hexanes are capable of combusting at a lower vapor concentration in air (1.15%) than bio n-butanol (1.4%). This fire hazard is exacerbated by hexanes’ higher vapor pressure, meaning it readily forms its flammable vapors through volatilization. In short, hexanes’ threshold for combustion is lower than bio n-butanol and it will reach its threshold faster due to its volatility. As a result, bio n-butanol can safely be used for extractions at higher temperatures than hexanes.
In addition to the safety benefits derived from the higher flashpoint, bio n-butanol is considered Generally Regarded As Safe (GRAS) by the Flavor and Extract Manufacturers Association of the United States (FEMA) and not a toxic solvent of concern. This designation means that bio n-butanol is a safe food ingredient. Also, hexanes are not FEMA GRAS. However, low concentrations (5-25 ppm) of hexanes are grandfathered into the GRAS classification as it was used in some applications, notably soy extractions, prior to FEMA GRAS becoming a recognized classification in 1958.
Background
Presently, only one domestic option is available for industrial supply of bio-derived n-butanol. Green Biologics produces bio n-butanol and bio acetone in Minnesota through what is called the ABE Fermentation Process. The process is named for the principle products of the fermentation: acetone, n-butanol, and ethanol (ABE). First industrialized by Chaim Weizmann in 1912, the ABE process uses clostridia bacteria to ferment both C5 and C6 sugars into high purity solvents. The ABE process fell out of use in the 1940s with the rise of the petrochemical industry; the last two industrial-scale facilities closed in South Africa and Russia in the 1980s. Green Biologics reintroduced the first commercial operation in 2015 with their facility in Little Falls, Minnesota. Advancements in modern technology, which finally allowed the ABE process to be competitive against petrochemical synthesis facilitated this resurgence of the ABE process.
Because the bio-derived solvents are produced using natural enzymes, the result is pure acetone, bio n-butanol and ethanol without the typical petrochemical impurities. This is also due to the benign feedstocks used in bio-based processes; unlike petrochemicals which use crude oil or natural gas as feedstocks, bio-based fermentations use plant-based sugars as feedstocks. The use of petrochemicals as feedstocks and heavy metals as catalysts are often high yielding processes, but typically are much less selective than enzymatic transformations, producing additional species, called impurities.
These impurities, such as iso-butanol, cumene, phenol or benzene, can cause process disruptions, necessitate regulatory oversite, and/or impact the health of final consumers. Despite its benign nature, acetone itself is traditionally made from benzene and propylene in petrochemical processes. California’s Proposition 65 can mandate rigorous regulatory review and final product labeling for products containing benzene and related aromatic species, even as trace impurities. For comparison, the production of traditional n-butanol from propylene, through the oxo process, results in coproducts such as iso-butanol and butyraldehydes, which are impurities in the final n-butanol product. The high-purity manufacturing of bio n-butanol by Green Biologics also generates lower emissions compared to petroleum-based alternatives. This more environmentally-friendly production occurs without sacrificing on performance as the molecules produced are chemically identical to the petrochemical analogs, only with fewer impurities. The feedstocks for fermentation products like bio n-butanol are also decoupled from the tight supply and volatility experienced in the petrochemical supply chain. This enables users to procure bio n-butanol without worrying about pricing swings in the oil market. While bio-based ethanol itself is not costly, ATF regulation and compliance add costs and ethanol simply does not have the same performance of bio n-butanol.
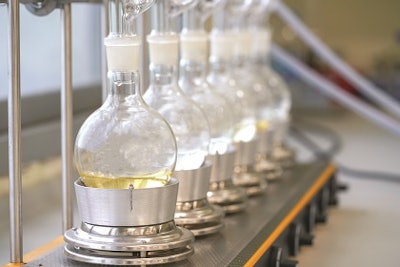
With fewer impurities, more stable pricing, a reliable process and supply, and strong performance characteristics, Green Biologics and Blue Marble wanted to validate their hypothesis that bio n-butanol is, in fact, a superior solvent for extractions. Therefore, the team tested it for three different applications including citrus, lavender and peppermint. These experiments produced data from which a comparison of the total oil yields and organoleptic profiles could be generated. Analysis of these comparative experiments showed potential cost savings for extract producers who typically use ethanol as their solvent.
Methods and Results
Extractions
Pure essential oils, which often have high commercial value, are produced from a wide array of plants. These oils are widely used in perfume, flavor and pharmaceutical industries. Several volatile terpenes found in essential oils have shown promise as jet- and missile-based tactical fuels. Essential oils are primarily plant-based secondary metabolites that exhibit strong aromatic properties that are made up of various compounds; these compounds can include: alcohols, terpenoids, phenols, aldehydes, ketones and esters. This article describes a procedure for retrieving essential oils and their associated compounds from peppermint (Mentha piperita), lavender and orange peels. Furthermore, we investigate the solvent extraction efficiencies and volatile terpene profiles of two widely used methods: steam distillation and Soxhlet extraction. Essential oils were extracted from dried leaves using four solvents: hexanes, bio n-butanol, ethanol and water. Water extraction of essential oil was accomplished using a conventional steam distillation method, whereas Soxhlet extraction (SE) was selected for hexane, bio n-butanol and ethanol extractions.
Soxhlet extraction is a simple method invented in 1879 by Franz von Soxhlet. Soxhlet extraction involves a unique recycling method to enhance typical solid-liquid contact between the solvent and solid plant material.1 In general, a SE apparatus consists of a water-cooled condenser, an upper reservoir which is filled with plant biomass, a siphon tube which pulls the liquid from upper reservoir cavity, and a lower reservoir distillation flask. When heated, the solvent boils producing vapors that condense and gradually fill the upper cavity. When the cavity fills, the siphon tube trips and fills the lower reservoir back into the distillation flask. This process is repeated until a complete extraction is achieved.
Soxhlet extraction is a common extraction technique as it has multiple advantages. First, through evaporation and subsequent cooling in the condenser, the sample is repeatedly brought into contact with fresh solvent; this prevents saturation of the solvent with extractable compounds. Furthermore, the temperature inside the SE apparatus is close to the boiling point of the solvent, which results in enhanced extraction kinetics for the entire process.
On the other hand, Soxhlet extractions exhibit several disadvantages in comparison to other extraction methods. The primary drawback is the amount of time required to extract plant material, which can range from several hours to approximately a day, depending on the sample matrix and amount of solvent used. In addition, the heating of the distillation flask can cause thermal degradation of the materials being extracted.
The following SE apparatus was utilized for extraction of essential oil from peppermint. A 1 L Soxhlet extraction reservoir was used with 100 g of shredded peppermint leaves. Cheesecloth was used to prevent plant material from entering the solvent vaporization and siphon tubes. A 3 L distillation flask, or lower reservoir, was filled with 2 L of solvent. The lower reservoir was then placed in a heating mantle to ensure steady reflux of the solvents. Because of the large size of the Soxhlet reservoir, an Allihn water-cooled condenser was used to return the solvent vapor phase to liquid. The time required to fill the upper reservoir with condensed solvent vapor and begin return to the flask was approximately 30 minutes. Total run time for each Soxhlet extraction was 6 hours, which entails 12 total refluxes of solvent through plant material back into the collection flask. The tables below show the various oil yields based on the conditions for Soxhlet and steam extractions (see T-2, T-3 and T-4).
After Soxhlet extraction, the extraction solvent was passed through a 0.25 μm filter via vacuum. The filtered extract was placed into a pre-weighed round bottom flask and evaporated until the solvent was completely removed. The round bottom flask was reweighed to determine oil yield, and the oil was extracted for use in GCMS analysis and organoleptics.
Gas Chromatography / Mass Spectrometry
Gas chromatography/mass spectrometry was utilized to determine the volatile profiles of oils that were extracted (see T-5, T-6 and T-7). For GCMS analysis, an Agilent 6890N GC was used with an Agilent 5973 MSD. The inlet temperature was 250 °C and the injection was splitless. Column was a Rxi-35Sil MS (30 m x 250 μm x 0.25 μm nominal) from Restek. The oven program was as follows: Starting oven temperature was 60 °C and held for 5 minutes. The temperature then was increased by 15 °C/min until it reached 230 °C. It was then held for 5 minutes at this final temperature. The total run time was 21.33 minutes. The scan parameters for the MSD start at 10 amu, and end at 350 amu. No solvent delay was used for the method.
Organoleptic Analysis
To assess any organoleptic differences in the four solvent extractions, a triad sensory evaluation of the peppermint extracts was performed. A panel of 17 members was utilized to perform this evaluation. 4,000 ppm of each extract were utilized to prepare each odor samples. The bio n-butanol extract served as the control and was compared against the water, hexanes and ethanol extracts. The 17 panel participants smelled three samples at seven different stations and recorded their results. Each station compared the control bio n-butanol sample to one of the other solvents. This method presented panelists with two samples that were the same and one that was different. Panelists were asked to smell or to taste all three samples and determine which sample differed from the rest. This test is often used in food research and development to determine if a change in manufacturing creates a noticeable sensory difference for consumers.
Organoleptic Panel Data from the Peppermint Extracts
The data reported that 82% of panelists could tell the difference between the hexanes peppermint extracts and the bio n-butanol peppermint extracts. These panelists often noted that the hexanes extract was more pungent. Approximately 91% of panel members could also tell the difference between the steam distilled peppermint extracts and the bio n-butanol peppermint extracts. In these comparisons, the panel members thought the water extracts had much stronger mint notes than either the ethanol or bio n-butanol extracts. This makes sense as the only extract that had a larger percent composition of menthol (a canonical mint fragrance) than bio n-butanol was water (note: despite this, the bio n-butanol yield was greater than 26 times higher, effectively producing more menthol, albeit at a lower concentration). However, only about 32% of the panel could accurately distinguish a difference in the ethanol peppermint extract and the bio n-butanol peppermint extract. During the ethanol and bio n-butanol comparisons the panelists often described observing non-mint notes, such as herbal and citrus notes in both the bio n-butanol and ethanol extracts.
These data demonstrate that a bio n-butanol peppermint extract could be substituted for an ethanol peppermint extract (see T-8). The sensory analysis panel indicated panelists had a difficult time determining the difference between the ethanol and bio n-butanol extracted peppermint. Conversely, panelists could effectively determine the difference between bio n-butanol extracted peppermint oil and both hexanes extracted peppermint oil and water extracted peppermint oil.
Ethanol and bio n-butanol both belong to a family of compounds named alcohols, meaning they both are carbon chains with a hydroxyl group (-OH) attached, whereas hexanes are a non-polar 6 carbon chain molecule. Because the structures of bio n-butanol and ethanol are similar, it can be surmised that both solvents extracted essential oil from the peppermint leaves in a similar way. A Hansen Solubility Parameter (HSP) plot is shown below to demonstrate how the various solvents can be compared based on polarity and hydrogen bonding (see F-1). Both bio n-butanol and ethanol are close together on the plot and circled in red. Bio n-butanol is slightly to the left of ethanol on the plot due its more nonpolar (or less polar) character. Additionally, hexanes are located far from both bio n-butanol and ethanol on the plot, which makes sense as the performance of hexanes differed from the alcohols. This allows us to conclude bio n-butanol is a favorable solvent to substitute for ethanol in alcohol-based extractions.
Conclusion
These results demonstrate that bio n-butanol extracts have a comparable odor profile to ethanol extracts but with much higher yields (nearly 3-4-fold more mass). These bio n-butanol extracts also have higher concentrations of fragrance and flavor molecules and can be produced at a lower cost. This allows extractors to get more valuable natural products out of their extraction dollars, which represents added value in their businesses. This trend holds as well for both citrus and lavender extractions. In the case of citrus extractions, the bio n-butanol and ethanol extract yields were comparable, but in the lavender oil extractions, a significant yield boost was seen when using bio n-butanol for the extraction. These additional examples highlight the versatility of bio n-butanol and broad applicability of the sustainable solvent’s outstanding performance. Further, bio n-butanol is a safe solvent to use in the industrial setting, with a lower vapor pressure and higher flashpoint than both ethanol and hexanes. Bio n-butanol, sustainably produced in the heart of America, is a powerful renewable extraction solvent that enables greater productivity, safer operations and cost savings.
References
- Rassem, H.H.A., A.H. Nour, and R.M. Yunus. Techniques for Extraction of Essential Oils from Plants: A Review. Australian Journal of Basic and Applied Sciences. 10(16) November 2016. 117-127.