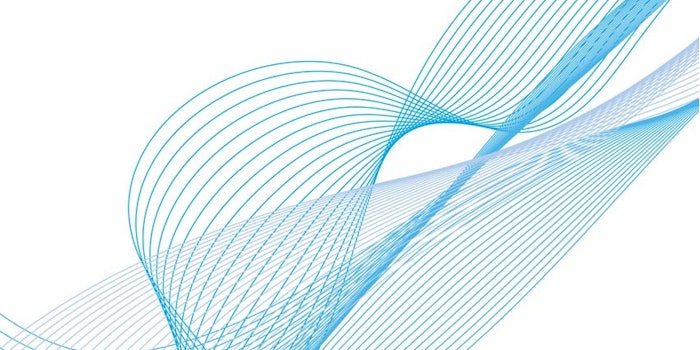
By Arne Teiwes, Process Engineer, Process Technology Food, Feed & Fine Chemicals at Glatt Ingenieurtechnik, Weimar, Germany
Delivery systems such as encapsulation technology help to control the release of flavors and fragrances. An intelligent gas flow management system with an inline condenser is key to successful processing: continuous spouted bed technology in closed cycle mode offers a solution for the heterogeneous-catalytic oxidation of volatile oils.
Manufacturing encapsulated essential oils in dry granular forms can be challenging, particularly regarding their tendency to agglomerate, their oil loss rates and complying with legal limits for volatile organic substances in industrial exhaust [1].
When it comes to long-lasting freshness, targeted release properties and other value adds, essential oils are increasingly being used in an encapsulated or free-flowing form. As such, microencapsulated fragrances have become an indispensable part of cosmetic, washing and cleaning products that release a particular scent at the required moment, such as during ironing, when opened, by temperature and also by body temperature or friction. Microencapsulation by spray granulation in a spouted bed process has subsequently become an important method in the production of these goods.
Particularly Gentle Process
Spouted bed technology is – like fluidized bed – based on the principle of fluidizing particles using upward-flowing process air. Differences lie in the geometric design of the process chamber, principle of air inlet and particle and air flow profiles, but both technologies can be used to spray granulate, agglomerate, coat and dry ingredients for high quality products. Overall, both technologies help to protect volatile substances and enhance handling and dosing.
For the gentle treatment of sensitive materials such as essential oils, spouted bed technology is the method of choice. It’s possible to work at very low temperatures with short residence times. And, solid particles of a defined size can be fluidized without a bottom screen and directed to the spraying nozzle. Moreover, the air velocity and temperature decline rapidly in the process chamber and allows the production of very fine, uniform particles that lose very little activity during drying.
Single-Step Combination
Spray granulation enables granule formation and release control to be done in a single step. Plus, homogeneously distributed substances can be embedded in a compact protection matrix. Alternatively, spray liquids can also be applied to carrier particles. Using an oil-in-water emulsion as a liquid starting material, spray granulation directly produces solid particles with a defined particle size, as well as a very fine oil distribution (see Figure 1).
Figure 1. Image courtesy of Glatt
A critical issue is the tendency of solids to agglomerate, particularly with solid matrices containing liquids. This is one area wherein spouted bed technology has proven itself to be a viable alternative to fluidized bed systems [2]. Commonly, single-pass processes are used to make oil-containing granules whereby up to 20 percent of the active substance tends to be lost, depending on the material system [3].
The loss, caused by thermodynamic equilibrium conditions – even during spray granulation – can be substantiated by sensitivity analyses with different volatile oils. What’s important, though, from both an economic and environmental perspective, is getting a higher oil recovery rate that ensures better product quality and decreases the consumption of valuable raw materials.
Part II will discuss the effects of redesigning air flow to yield higher oil concentrations.
References
1. H Strass, Komplexe Gemische. Analysenmethode für ätherische Öle, GIT Laborfachzeitschrift 56. (1) 19–21 (2012)
2. O Gryczka, Untersuchung und Modellierung der Fluiddynamik in prismatischen Strahlschichtapparaten, Dissertation, Technical University of Hamburg-Harburg, Germany (2009)
3. Bundesministerium für Umwelt, Naturschutz und Reaktorsicherheit, Germany, Erste Allgemeine Verwaltungsvorschrift zum Bundes–Immissionsschutzgesetz - Technische Anleitung zur Reinhaltung der Luft, TA-Luft, July 24, 2002 (2002)