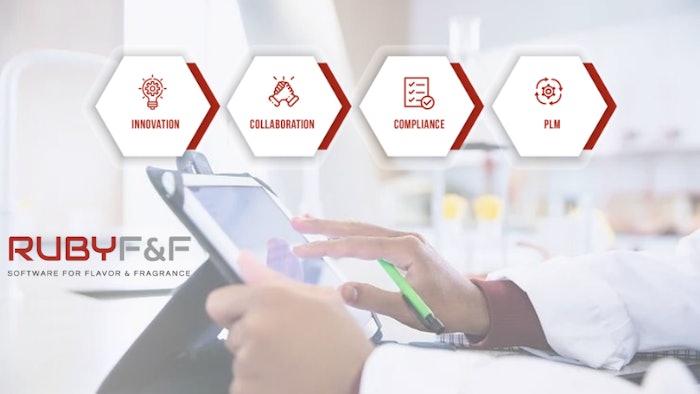
Author: Susan Grace, Ruby Vision Global Solutions Pvt Ltd
Being a creative industry, perfumers and flavorists are naturally protective of their intellectual property and many still rely heavily on tools like Excel with data stored locally.
Pain points with this approach are many and they only increase as companies grow. For example:
- Checking a formula’s regulatory compliance (e.g., IFRA, EU/USFDA Allergens) is tedious.
- Tracking and controlling formula versions and BOM versions is difficult.
- Too much time spent on emails, calls and meetings instead of creating or promoting.
- Delays or mistakes due to difficulty in tracking what products have been sampled to which customer, price quoted, documents submitted, etc.
- Lack of access to real time data on project status, submission details, product cost, etc.
- Issues with multiple versions of raw material or product data.
- Delays caused by expiring raw material certificates.
- Difficulty in accessing required information when key people go on leave or work from home.
- Traceability issues.
- Difficulty in complying with ever increasing certification requirements.
If you can relate to one or more of these pain points, this article is for you!
Here are 10 stand-out benefits that flavor and fragrance companies experience by implementing an effective, integrated software solution for flavor and fragrance PLM*:
- Data security: All data is held on secure servers, making centralized back-up easy and giving users access only to the data they need for their job via role-based permissions systems.
- Single source of approved raw material and product data: This reduces errors and greatly improves productivity.
- Auto-Traceability: Will apply to your products down to the raw material batch level.
- Formulate to specification and budget: Dynamic calculations provide easy access to important information as you formulate, such as product input cost, allergen status, IFRA compliance, legal status, nutrition data, product specs, etc. More information
- Automated tracking: Applies to all changes, formula and BOM versions, sample submissions, quotations, customer feedback, product specs, quality control data, etc.
- Reduces risks: Automating many complex and tedious calculations, regulatory compliance checking, document generation and approval process will help mitigate risks. More information
- Faster on-boarding of new staff: This includes easier compliance with certification/audit requirements.
- Reduced time to market: Automated collaboration and any-time access to the data your team needs to work effectively will reduce time to market.
- Faster growth: Organizations are able to scale-up much faster to deliver on market opportunities.
- Increased productivity and job satisfaction: PLM software enables your team to better focus on product innovation by eliminating a lot of time-wasting manual tasks. More information
It is true that pain points are also experienced when implementing the best of software solutions. A successful implementation requires research and evaluation of solutions against an organization’s needs, and investment of time and money in working with a solution provider on data migration, aligning processes and getting staff trained. But investing in overcoming these short-term pain points sets an organization up for sustained growth and immeasurable long-term benefits.
On the other hand, continuing to get by with outdated methods and systems which are not designed for a specific purpose damages a company’s competitiveness and makes scaling-up for serious growth almost impossible. Furthermore, reliance on inappropriate tools makes regulatory compliance an increasing burden and increases the risk of non-compliance as the company grows. Status quo can be more costly than you think!
*What is Product Lifecycle Management (PLM)?
In relation to flavor and fragrance, PLM refers to management of the data and processes used in the development, testing, manufacturing, sampling and sale of products across their lifecycle. A good PLM software will also facilitate automated regulatory checking and complete traceability.
Disclaimer:
The above paid-for content was produced by and posted on behalf of the Sponsor. Content provided is generated solely by the Sponsor or its affiliates, and it is the Sponsor’s responsibility for the accuracy, completeness and validity of all information included. Perfumer & Flavorist takes steps to ensure that you will not confuse sponsored content with content produced by Perfumer & Flavorist and governed by its editorial policy.