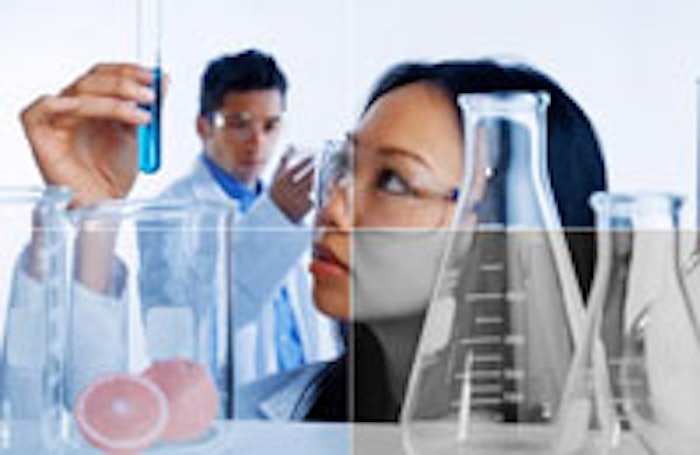
Quality sells. It can make or break your company. You want to find the optimal way to produce the best product at the lowest cost. But what are your choices?
Spreadsheets can help give you basic "what if" information, but they do not tie back to the customer's specification. You risk reworking batches rejected by the customer. Not to mention no audit trail for substitutions.
Separate software for formulas and ERP suffers from the disconnection. What if your inventory does not reflect the formula it was cost with? When you quote your customer, you have to guess and get priced out of the marketplace!
Some systems do not go beyond a simple formula. Calculations done outside a system risk errors and show no history of what may have been forgotten in the computation. How will you sell for the optimal price if you only know "average cost?"
Quality has a price tag. You need to contain costs through proper planning. How will you plan production if each formula does not have raw material, equipment, labor, byproduct and overhead costs at each step? Do you know if your production successfully adapts to customer demands?
ProcessWare™ ERP ties all of your products together with the specifications and associated costs at every stage. The production team knows exactly what the customer's requirements are, and which inventory meets those requirements. Sales can perform “what-if” analysis to meet customers' changing needs and maximize revenue. Raw material substitutions and byproduct handling let production choose the optimal formula for the lowest cost of manufacture!
Expanding Business With ProcessWare™ ERP
When Chemlumina, an innovator in the Flavor & Fragrance industry, saw its business rapidly expanding, it realized that it needed a more sophisticated business approach to support this growth.
In less than one year of using the new system, Chemlumina has realized significant benefits to its business. "With Processware ERP we are much more efficient and productive. While we have doubled our business we haven't had to hire additional employees; that's a tremendous accomplishment." - Bill Fylak, president, Chemlumina
Read the full case study to find out how they did it and contact us to learn how you can too.
Disclaimer:
The above paid-for content was produced by and posted on behalf of the Sponsor. Content provided is generated solely by the Sponsor or its affiliates, and it is the Sponsor’s responsibility for the accuracy, completeness and validity of all information included. Perfumer & Flavorist takes steps to ensure that you will not confuse sponsored content with content produced by Perfumer & Flavorist and governed by its editorial policy.